- Cobot Spotlight Newsletter
- Posts
- How a Sensor Manufacturer Hit 97% Productivity In Repetitive Production – Hassle Free!
How a Sensor Manufacturer Hit 97% Productivity In Repetitive Production – Hassle Free!
What happens when you give repetitive, quality-sensitive tasks to a cobot? You go from great to exceptional. Brimind saw this firsthand, boosting quality, slashing scrap, and hitting 97% productivity using ABB’s GoFa cobots.
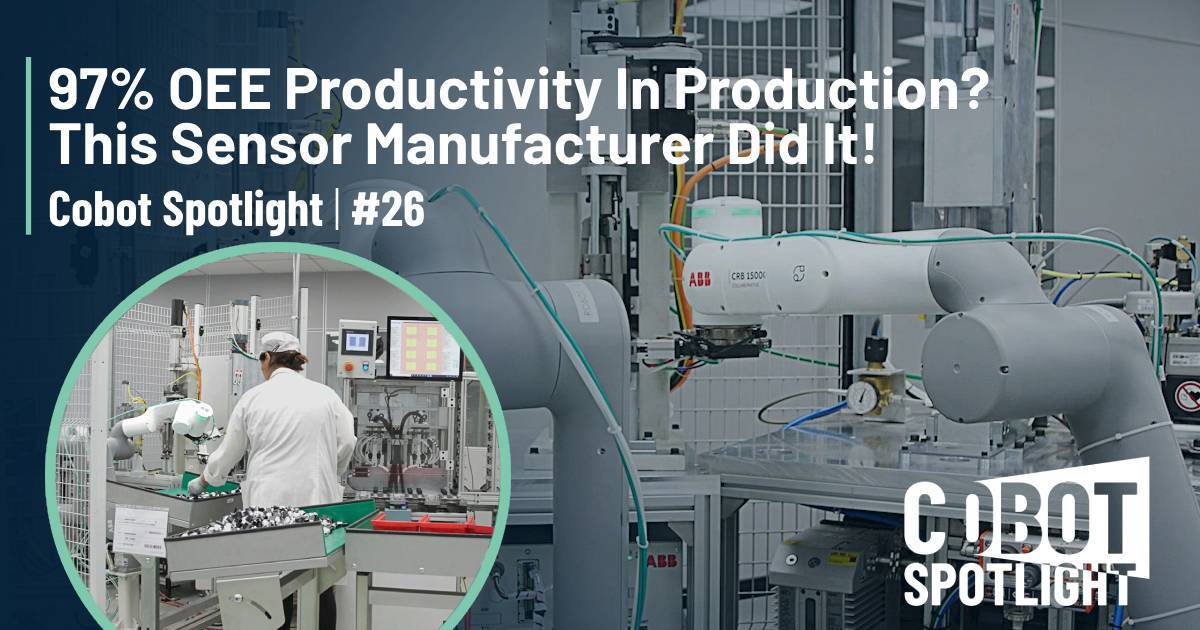
Did someone forward this newsletter to you? Subscribe to our weekly Cobot Spotlight newsletter where we analyze success stories just like this one!
Brimind is an Italian manufacturer of high-precision pressure and temperature sensors for the automotive industry.
As a certified Tier 1 supplier, they must meet strict IATF 16949 standards. Translation? Every sensor has to be consistent, accurate, and flawless.
That’s tough to guarantee with human-only assembly, especially when productivity fluctuates, and even minor errors mean scrap.
Brimind identified two machine-tending tasks better suited for robotics, but they still needed to maintain human presence and activity… Which is a job for cobots, of course!
So they brought in two ABB GoFa collaborative robots to handle sensor assembly and prep for testing. The result? Better quality, higher speed, and a line that basically runs itself.
Cobot Brand | Supplier | Application |
---|---|---|
ABB | ABB | Machine tending, part assembly |
The Key Problems | How the Cobots Were Implemented | The Results |
Fluctuating operator productivity and human error during sensor assembly. Needed better quality and more consistent output. | Two GoFa cobots now assemble the sensor body, close it, and pass it to the leak test station. The whole process runs with little human interference. | Reached 97% productivity. Improved consistency. Reduced scrap to nearly zero. Freed up staff for more valuable tasks. |
Why The Need To Automate?
Before cobots, Brimind’s production line was mostly manual. Operators were assembling the electronics and mechanical body of the sensor before sending it off for testing.
But small parts and tight tolerances?
It only takes a few minor mistakes to cause production issues.
To top it off, they had to improve the production consistency. Human productivity goes up and down, and unlike robots, humans can make mistakes.
“These stations were previously served by operators, but due to human errors, the quality level was not as high as we wanted. The productivity of human operators could also fluctuate. By introducing automation, our objective was to improve and maintain a stable quality level and improve the productivity of the line.”
Choosing The Solution… What Drove Them To Cobots?
Birmind already used robotics for assembly, but this time they needed something… More flexible. More modular.
Since their parts can require reprogramming, they needed a robotic system that can quickly be readjusted to fit the needs of another sensor part. So, traditional robotics wasn’t the best choice.
The production processes they wanted to automate were already separated into modular stations with their own subprocesses. So, cobots could easily be included as an “add-on” to their respective stations, without hard changes or modifications of safety barriers required by traditional robotics.
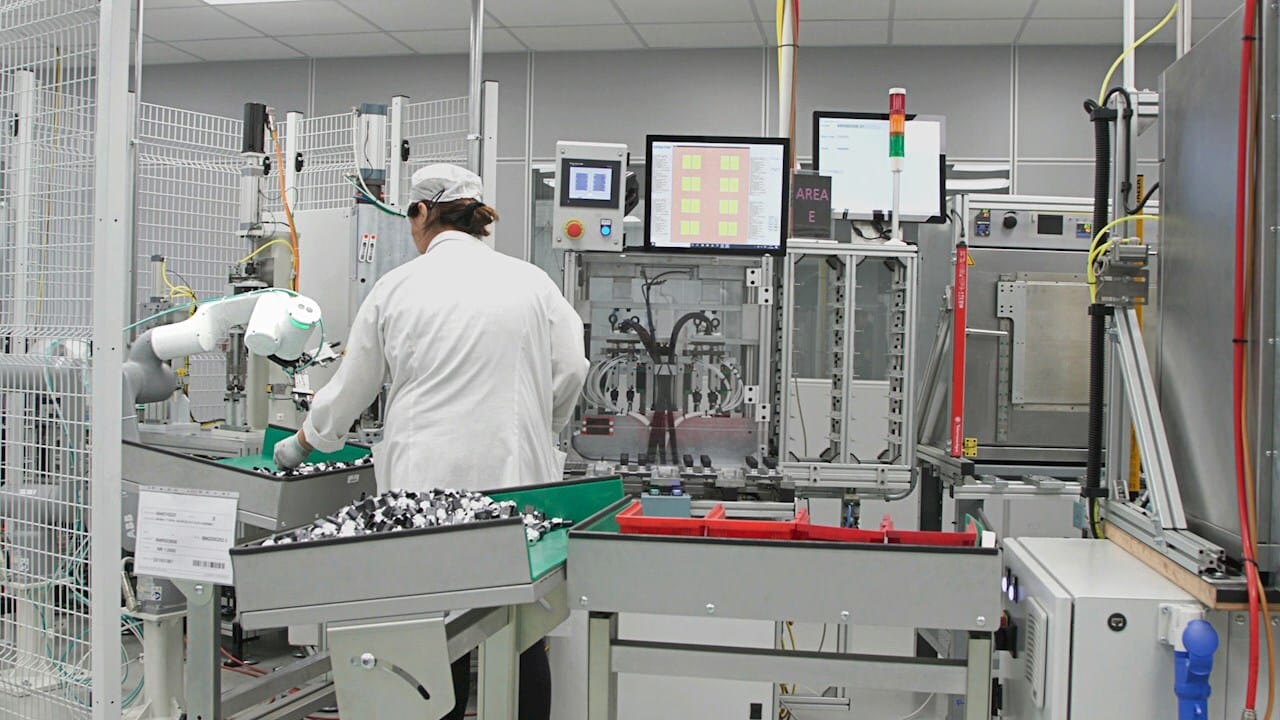
Brimind staff working with the ABB cobot that’s integrated into the modular cell. Image source.
“By introducing automation using collaborative robots, we maintained this modularity because there is no need for the huge protective barriers to separate the existing stations or disturb the link between those three stations and the rest of the line,” said Leo.
ABB’s GoFa collaborative robots were up to the task.
Brimind installed two GoFas, one to assemble the electronics and the body of the part before moving it to the second station, where the second GoFa secures the assembly and moves it for leak testing.
Each part is handled with care and consistency, every time. No skipped steps or fatigue.
Easy Deployment And Quick Results
Brimind handled the cobot setup themselves, with support from ABB when needed. The cobots were running in no time, requiring only real-time adjustments where necessary.
Their manual sensor assembly achieved an OEE (Overall Equipment Effectiveness) of close to 90%. Not bad, but in the automotive industry, they benefit greatly from raising that number.
At first, Brimind hoped to achieve 95% productivity.
However, ABB’s GoFa cobots helped them shoot over and land at 97% !
They also:
Reduced scrap
Improved process repeatability
Freed up operators for more valuable work
Gained flexibility for future lines and product variants
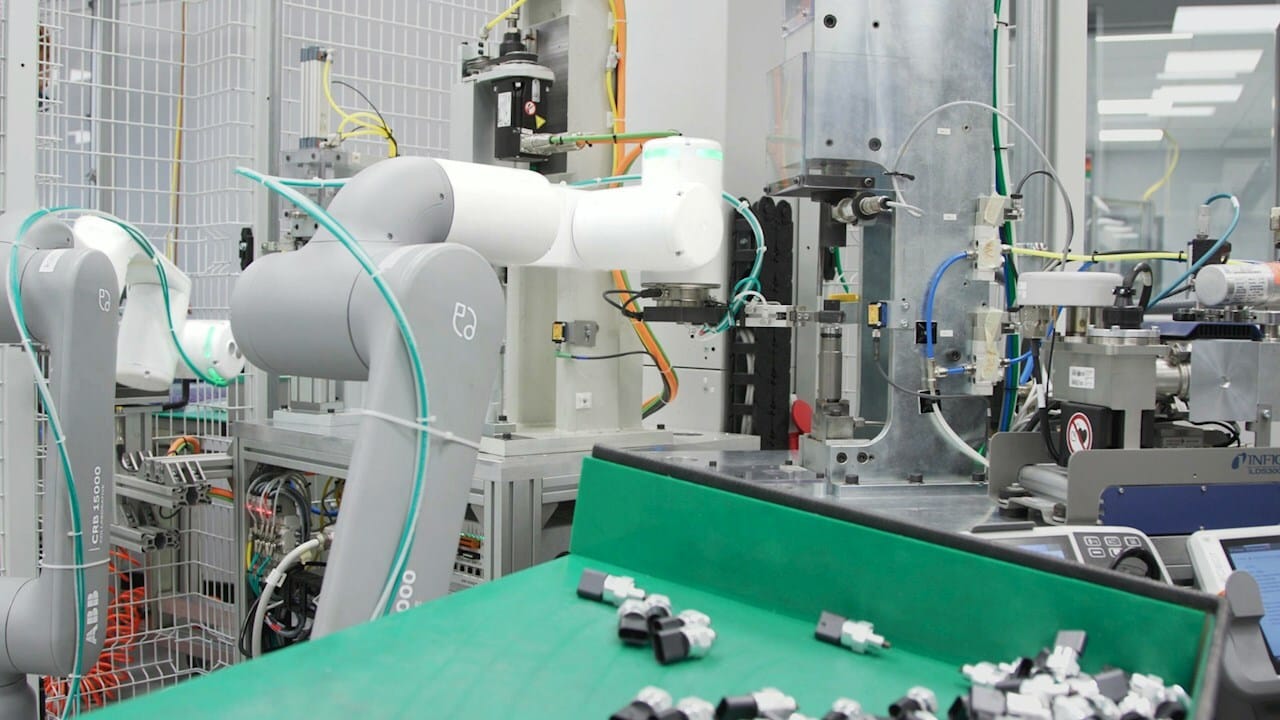
ABB GoFa Cobots working on sensor assembly in the Brimind facility. Image source.
“The GoFa cobots bring a lot of flexibility and repeatability to the process line – they can be used to handle a wide variety of pieces and offer the ability to produce a small sample of products with the same quality as large-scale mass production.”
The cobots’ easy programming and flexibility help them use their abilities wherever necessary, with minimal effort.
Found this newsletter valuable? Share it with your peers to amplify the impact of cobots in our lives!
“With just a button I can move the robot to a new position or change its configuration just with my hand rather than by moving it with the controller. This means that we can limit the stoppage time when we need to reprogram the robot,” Bini adds.
Learn more about Brimind's success with ABB cobots below:
Do you have a success story to share? Send us an email! We want to hear about it!
Enjoy your week!
The Cobot Spotlight Team